町工場がIoTで生産業務を大幅に改善。約3億円の設備投資と約1億円の労務費削減
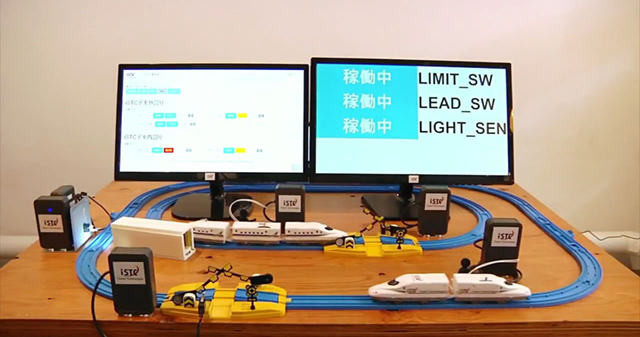
昭和の機器も含めIoTで生産ラインを見える化
IT分野の調査・助言を提供するガートナージャパンは2017年4月26日~28日の3日間、「ガートナー ITインフラストラクチャ & データセンター サミット 2017」を開催。2日目のゲスト基調講演には、旭鉄工 代表取締役社長 兼 i Smart Technologies 代表取締役社長 CEOの木村哲也氏、およびi Smart Technologies 執行役員 COOの黒川龍二氏が登場し、「町工場でも成果の出せるIoT! ~昭和の機械も接続~」をテーマに講演しました。
旭鉄工は1941年に木村鉄工所として創立され、1943年よりトヨタ自動車工業との取引を開始。現在に至るまでエンジン用部品、トランスミッション用部品、ブレーキ部品、サスペンション用部品など、トヨタ自動車向けの自動車部品を中心に幅広い製品を製造しています。2015年度の売上高は158億円で、従業員数は480名。国内拠点として、本社工場と西尾工場の2拠点、海外拠点としてタイの1拠点で、ものづくりを展開しています。
現在、旭鉄工では全社一丸となってトヨタ生産方式に基づく“カイゼン”を推進。その一環として、IoTを活用した生産ラインの稼働状況の“見える化”に取り組んでいます。木村氏は「生産ラインが動いているのか止まっているのか、目標を達成しているのか達成していないのかなどの状況を、スマートフォンでリアルタイムに把握できます。これにより、3億円以上の設備投資と、1億円以上の労務費を削減できました」と語ります。
このIoTを活用した“町工場でも成果の出せる”仕組みが、「製造ライン遠隔モニタリングサービス」です。それでは、製造ライン遠隔モニタリングサービスはいかにして実現に至ったのでしょうか?
欲しいものは自分たちで作るのが1番
旭鉄工がIoTへの取り組みを開始したのは2014年からです。2014年に“第1世代”を構築し、2015年に第2世代、2016年に第3世代を構築しています。今後さらに、第4世代、第5世代へと進化を続ける予定です。IoT活用の背景を黒川氏は、「“人には付加価値の高い仕事を”という思いがあります。生産実績と停止時間の把握は自動化し、人は改善に集中する。この仕組みにIoTが活用できないかと考えました」と話します。
そこで、さまざまな展示会やセミナーなどに参加して、IoTソリューションの調査を実施しました。その結果、(1)大がかりでコストがかかる、(2)既存(昭和)の設備が使えない、(3)データが活用しにくい、という3つの課題がありました。黒川氏は「一般的なIoTソリューションは数百万円~数千万円かかる仕組みが多く、中小規模の町工場に導入できるものではありませんでした」と話します。
旭鉄工には約400の生産工程があり、設備にすると数千台になります。この設備の50%は20年以上使用しており、さらに“昭和の設備”が10%あります。この昭和の設備を現存のIoTソリューションと連携するのは困難でした。また欲しいデータの取得が困難で、データを活用できませんでした。そこで「欲しいものは自分たちで作るのが1番」という社長の言葉に基づき、製造ライン遠隔モニタリングサービスの構築が開始されました。
開発コンセプトは「秋葉原で買える部品で欲しいものを自作する」こと。まず考えたのが、ARMベースのシングルボードコンピュータである「Raspberry Pi(ラズベリー パイ)」を利用して、必要なセンサーを開発することでした。黒川氏は「木村社長から“初期投資を安く”というテーマが与えられました。そこで、お金をかけずにシステムを構築するためにはどうすればよいかを考えました」と話します。
「検討した結果、まずクラウドを利用することを決めました。自社サーバはあるものの、調達から構築、運用管理までコストがかかることから、すべてのデータをクラウドに格納し、スマートフォンやPCを利用することで、専用品の購入を不要にしました。さらに乾電池や無線LANを利用することで、配線工事を不要にしました。これにより完成したのが、“第1世代”です」(黒川氏)
第1世代は単純に正常・異常のデータを取得する仕組みでした。生産設備に送信機を取り付けて、無線で信号を飛ばし、受信機で受け取って、そのデータをクラウド上に格納し、処理したデータをスマートフォンなどで参照できるようになっています。黒川氏は「第1世代では、(1)稼働時間と(2)停止時間という2つのデータが見えるようになりました」と話します。
しかし稼働時間と停止時間が見えるだけでは、業務の改善にはつながりません。黒川氏は「IoTは一般的には“Internet of Things”の略ですが、社内では“ITからOT(Operational Technology)へ”と呼んでいます。つまり、運用を重視しようと考えました。そこで毎日、“ラインストップ会議”を開催し、停止の要因や対策方法などを話し合いました。それでも、なかなか停止時間が減らない状況でした」と話します。
停止したのがわからないから改善のしようがない
現場に話を聞くと、「停止したのがわからないから、改善のしようがない」という回答。そこで、設備の異常を表示する「あんどん」を設置すればよいと考えました。しかし、あんどんの設置には、専用の表示装置を取り付ける高所作業や有線LANの設置などが必要で、ラインを変更したときには有線LANのやり直しも必要になるなど、かなりのコストがかかります。考えた結果、誕生したのが「iスマートあんどん」と呼ばれる仕組みでした。
iスマートあんどんは、ラインに「セレクトスイッチ」を取り付け、ラインの状況をセンサー子機からセンサー親機に無線で送信。センサー親機で受け取ったラインの状況は、汎用のモニターに表示するほか、取り付けられたスピーカーにより音声でも警報します。黒川氏は「汎用モニターや無線LANを利用したことで、高所作業やLAN工事が不要となり、一般的なあんどんに比べて10分の1のコストで導入できるようになりました」と話します。
iスマートあんどんにより、停止時間は低減できたのですが、生産個数はなかなか増えませんでした。調べてみると、製品が1個できる時間である「サイクルタイム」にばらつきがありました。生産個数を増やすには、ラインの稼働時間とサイクルタイムの把握が重要です。そこで正確なサイクルタイムを把握するための仕組みとして、“第2世代”となる「サイクルタイムモニター」の開発がスタートします。
黒川氏は「サイクルタイムモニターは、シグナルタワーに取り付けた光センサーや、シグナルタワーのない昭和の機械に取り付けた磁気センサーのオン/オフによるパルス信号が送信機から送信され、受信機は受け取ったデータをクラウド上に蓄積します。クラウド上のデータはスマートフォンで確認することができます。これにより、生産個数やサイクルタイム、停止時刻・時間を、リアルタイムに把握できます」と話します。
サイクルタイムモニターを実現したことによる業務改善の効果としては、西尾工場の切削ラインの出来高が69%向上したほか、工程内の不良率を20分の1に低減しています。また全社での効果は、設備投資額を累計で3億3000万円削減したほか、製造工数を4%(2万時間)低減しています。4%の設備工数削減を労務費に換算すると、1億円以上の削減効果を実現したことになります。
中小製造業の生産性向上のお手伝いをしたい
旭鉄工では第2世代まで自社開発で対応してきました。しかしシステムが複雑化してきたために、これ以上、自社開発で拡張することは困難でした。黒川氏は「第3世代の開発については専門家に任せようということになり、レッド・ハットとの協業で開発することを決めました。レッド・ハットをパートナーに選定した理由は、ITの素人である我々にも、わかりやすい言葉でサポートしてもらえたからです」と話します。
完成した“第3世代”は、第1世代、第2世代の機能を統合し、さらに人工知能(AI)を搭載することで、「製造ライン遠隔モニタリングサービス」として構築されています。AIを搭載することで、設備が正常に稼働しているか、異常なのかといった状態を瞬時に判断できるようになりました。この製造ライン遠隔モニタリングサービスを、拡販することを目的とした会社「i Smart Technologies」が2016年9月に設立されています。
木村氏は「当たり前ですが、IoTの導入は“目的”ではなく“手段”です。どこのIoTシステムを使っても問題は改善できますが、製造ライン遠隔モニタリングサービスは、現場で使いやすく鍛え上げられたシステムで、より効果が期待できます。問題が見えても対策方法が分からない場合には、サポートも提供します。町工場でも成果の出せるIoTで、日本の中小製造業の生産性向上のお手伝いをしたいと思っています」と話しています。
「製造ライン遠隔モニタリングサービス」のデモビデオ。
( 出典:i Smart Technologies製品紹介サイト:http://istc.co.jp/service/index.html )